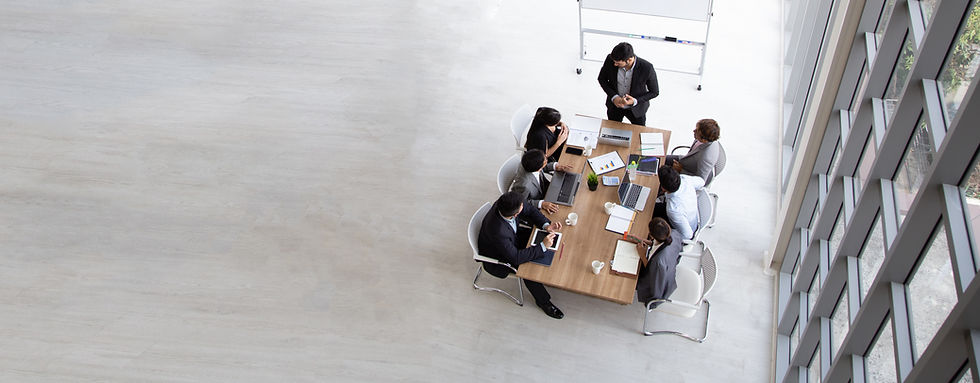
Why Lean Manufacturing & Operational Excellence Matter Today
- In a fast-changing market, organizations must stay agile, efficient, and customer-focused. Lean Manufacturing and Operational Excellence provide the foundation to reduce waste, improve productivity, and foster a culture of continuous improvement. We leverage popular frameworks such as Lean Six Sigma, Kaizen, Value Stream Mapping, and 5S workplace, Just-In-Time (JIT) production to drive efficiency and continuously improvement. These comprehensive approaches ensure that your operations remain competitive and resilient in the face of industry challenges.

Overcoming Key Challenges to Operational Efficiency
Inefficiencies in Processes:
- Unnecessary steps, bottlenecks, and redundant activities hinder productivity.
Our Solution:
We identify and eliminate non-value-adding activities using Value Stream Mapping, streamlining workflows to maximize efficiency.
High Operating Costs:
- Inefficient use of resources leads to rising costs, affecting your bottom line.
Our Solution:
We incorporate Lean Six Sigma, Just-In-Time (JIT) production and 5S workplace organization, to help minimize waste and optimize resource utilization.
Case Study: Operational & Strategy Assessment for Manufacturing Footprint Optimization
- In 2024, we were engaged by the leadership of a global paper products company’s consumer packaging division to assess its manufacturing operations and optimize its footprint in response to changing market conditions. The division was facing excess manufacturing capacity, which was negatively impacting profitability. Over a multi-phase assessment, our team analyzed manufacturing data across all plants and developed a mathematical model of the entire operation. We also incorporated demand forecasts from key industrial sectors, including pharmaceuticals, beauty products, and confections, to evaluate multiple manufacturing footprint scenarios. As a result of our analysis, we identified an optimized manufacturing footprint configuration projected to generate cost savings between $6M and $10M. Our recommendations positioned the client for future demand fluctuations while improving overall operational efficiency.
Misalignment Between Strategy and Execution:
Disconnected operations and unclear goals can lead to suboptimal performance.
Our Solution:
We align operational processes with your strategic goals, ensuring measurable outcomes and consistent performance improvements.
Product Design not Cost Optimized:
Product designed with features for functions that are not necessary. Or design choice not cost optimized.
Our Solution:
We apply Value Analysis and Value Engineering principles to come up with cost optimized design, reducing COGS and improve profit margin.
Our Process
Transforming Operations Through Proven Methodologies
-
Operational Assessment: Conduct a thorough evaluation of your current processes to identify inefficiencies and improvement opportunities.
-
Customized Strategy Development: Develop tailored Lean Manufacturing and Operational Excellence plans that align with your unique business needs.
-
Implementation of Lean Tools: Apply tools like Value Stream Mapping, Kanban, and Root Cause Analysis to optimize operations and reduce waste.
-
Continuous Improvement Activation: Establish frameworks for ongoing monitoring and incremental improvements, ensuring long-term success.
-
Employee Training & Engagement: Equip your teams with the skills and mindset needed to sustain Lean practices and drive continuous improvement.
-
Value Analysis & Value Engineering: Conduct a structured and systematic analysis of your product design to come up with the most cost optimized solution.

Case Study: Cost-Effective Product Redesign Using Value Analysis & Engineering
- Recently, we were hired by an industrial water pump company to help regain market share by developing a more competitive product. The company needed to reduce production costs while maintaining performance and reliability to compete effectively in the industry. We conducted a Value Engineering workshop, analyzing the client’s existing product alongside competitor offerings. Through structured brainstorming and engineering assessments, we generated innovative design concepts for the next-generation pump. As a result, we developed a new pump design that reduced material costs by 37% compared to the previous generation, enabling the client to enhance its competitive position while maintaining profitability.
What Makes Us Different?
Delivering Excellence with a Tailored Approach
-
Data-Driven Solutions: We use analytics and performance metrics to guide decision-making.
-
Industry Expertise: Our team brings extensive experience across manufacturing, automotive, and other key sectors.
-
Proven Frameworks: We implement globally recognized methodologies like Lean Six Sigma and Kaizen to ensure success.
-
People-Centric Approach: We prioritize workforce engagement to drive sustained improvements.
Key Benefits of Our Approach
-
Up to 40% reduction in operational costs.
-
Enhanced productivity through streamlined workflows.
-
Improved customer satisfaction with faster delivery and higher quality.
-
A culture of continuous improvement that fosters innovation and adaptability.